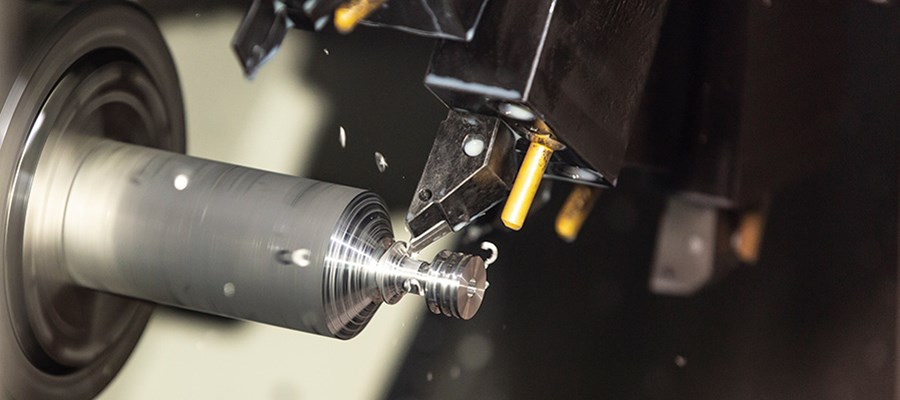
პირველი, რაზეც უნდა ვისაუბროთ, არის ტიტანის შენადნობის დამუშავების ფიზიკური ფენომენი. მიუხედავად იმისა, რომ ტიტანის შენადნობის ჭრის ძალა ოდნავ აღემატება იმავე სიხისტის ფოლადს, ტიტანის შენადნობის დამუშავების ფიზიკური ფენომენი ბევრად უფრო რთულია, ვიდრე ფოლადის გადამამუშავებელი, რაც ზრდის ტიტანის შენადნობის დამუშავების სირთულეს.
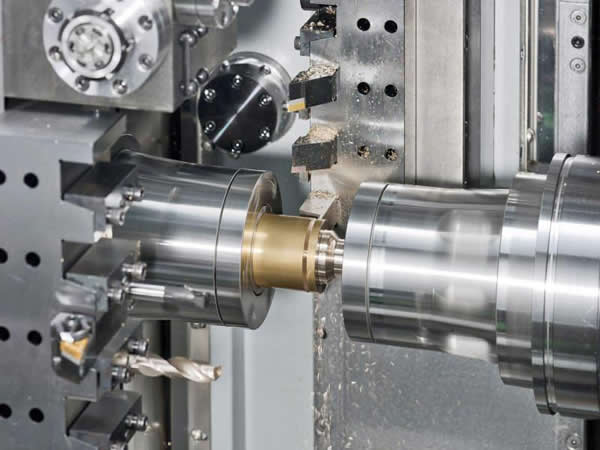
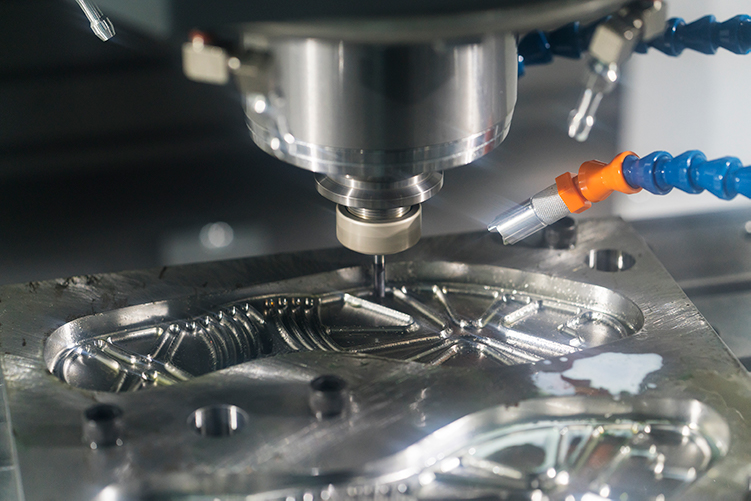
ტიტანის შენადნობების უმეტესობის თბოგამტარობა ძალიან დაბალია, მხოლოდ ფოლადის 1/7 და ალუმინის 1/16. ამრიგად, ტიტანის შენადნობების ჭრის პროცესში წარმოქმნილი სითბო სწრაფად არ გადაეცემა სამუშაო ნაწილს ან წაღებული იქნება ჩიპებით, მაგრამ დაგროვდება ჭრის ზონაში და წარმოქმნილი ტემპერატურა შეიძლება იყოს 1000 °C ან მეტი. , რაც გამოიწვევს ხელსაწყოს საჭრელი კიდის სწრაფ ცვეთას, ჩიპს და ბზარს. ჩაშენებული კიდის ფორმირება, ნახმარი კიდის სწრაფი გამოჩენა, თავის მხრივ წარმოქმნის მეტ სითბოს ჭრის არეში, რაც კიდევ უფრო ამცირებს ხელსაწყოს სიცოცხლეს.
ჭრის პროცესში წარმოქმნილი მაღალი ტემპერატურა ასევე ანადგურებს ტიტანის შენადნობის ნაწილების ზედაპირის მთლიანობას, რის შედეგადაც მცირდება ნაწილების გეომეტრიული სიზუსტე და სამუშაო გამკვრივების ფენომენი, რაც სერიოზულად ამცირებს მათ დაღლილობის სიძლიერეს.
ტიტანის შენადნობების ელასტიურობა შეიძლება სასარგებლო იყოს ნაწილების მუშაობისთვის, მაგრამ ჭრის პროცესში, სამუშაო ნაწილის ელასტიური დეფორმაცია ვიბრაციის მნიშვნელოვანი მიზეზია. ჭრის წნევა იწვევს "ელასტიური" სამუშაო ნაწილის მოშორებას ხელსაწყოსგან და აბრუნებს ისე, რომ ხელსაწყოსა და სამუშაო ნაწილს შორის ხახუნი უფრო დიდი იყოს, ვიდრე ჭრის მოქმედება. ხახუნის პროცესი ასევე წარმოქმნის სითბოს, რაც ამძიმებს ტიტანის შენადნობების ცუდი თბოგამტარობის პრობლემას.
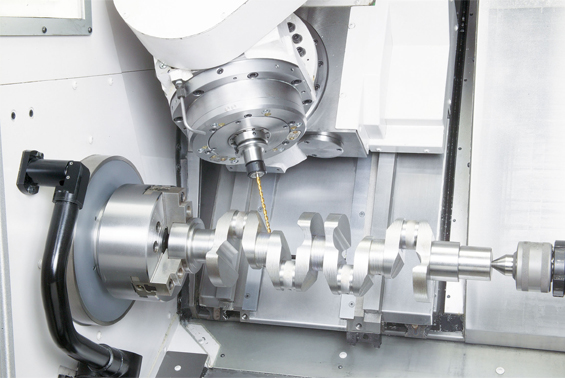
ეს პრობლემა კიდევ უფრო სერიოზულია თხელკედლიანი ან რგოლისებრი ნაწილების დამუშავებისას, რომლებიც ადვილად დეფორმირდება. ტიტანის შენადნობის თხელკედლიანი ნაწილების მოსალოდნელი განზომილების სიზუსტით დამუშავება ადვილი საქმე არ არის. იმის გამო, რომ როდესაც სამუშაო ნაწილის მასალა ხელსაწყოს მიერ დევს, თხელი კედლის ადგილობრივმა დეფორმაციამ გადააჭარბა ელასტიურ დიაპაზონს და ხდება პლასტიკური დეფორმაცია, ხოლო მასალის სიმტკიცე და ჭრის წერტილის სიმტკიცე მნიშვნელოვნად იზრდება. ამ დროს, ადრე განსაზღვრული ჭრის სიჩქარით დამუშავება ძალიან მაღალი ხდება, რაც შემდგომში იწვევს მკვეთრი ხელსაწყოს ცვეთას. შეიძლება ითქვას, რომ „სითბო“ არის „ძირეული მიზეზი“, რაც ართულებს ტიტანის შენადნობების დამუშავებას.
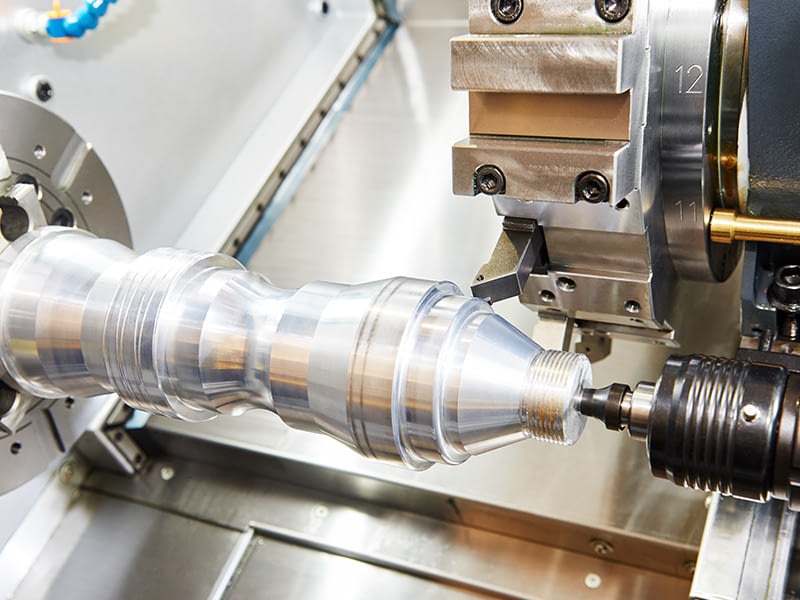
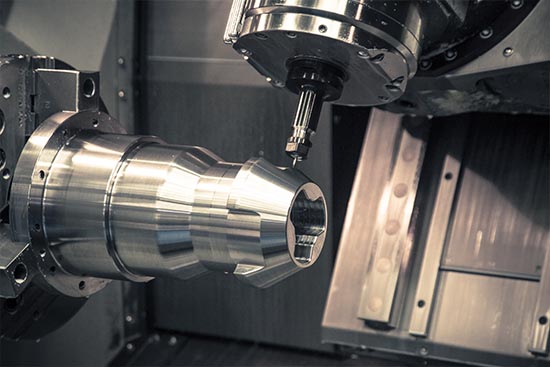
როგორც ლიდერი საჭრელი ხელსაწყოების ინდუსტრიაში, Sandvik Coromant-მა გულდასმით შეადგინა ტიტანის შენადნობების დამუშავების პროცესის ნოუ-ჰაუ და გაუზიარა მთელ ინდუსტრიას. Sandvik Coromant-მა თქვა, რომ ტიტანის შენადნობების დამუშავების მექანიზმის გააზრებისა და წარსული გამოცდილების დამატების საფუძველზე, ტიტანის შენადნობების დამუშავების ძირითადი პროცესის ნოუ-ჰაუ შემდეგია:
(1) დადებითი გეომეტრიის ჩანართები გამოიყენება ჭრის ძალის შესამცირებლად, ჭრის სითბოს და სამუშაო ნაწილის დეფორმაციის შესამცირებლად.
(2) შეინახეთ მუდმივი კვება, რათა თავიდან აიცილოთ სამუშაო ნაწილის გამკვრივება, ინსტრუმენტი ყოველთვის უნდა იყოს კვების მდგომარეობაში ჭრის პროცესში და რადიალური ჭრის რაოდენობა ae უნდა იყოს რადიუსის 30% დაფქვის დროს.
(3) მაღალი წნევის და დიდი ნაკადის საჭრელი სითხე გამოიყენება დამუშავების პროცესის თერმული სტაბილურობის უზრუნველსაყოფად და ხელს უშლის სამუშაო ნაწილის ზედაპირის გადაგვარებას და ხელსაწყოს დაზიანებას ზედმეტი ტემპერატურის გამო.
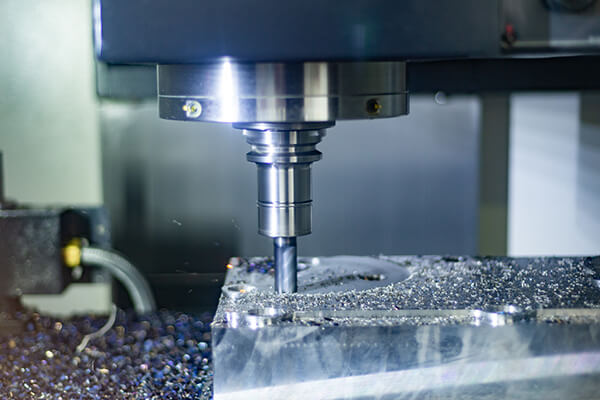
(4) შეინახეთ დანის კიდე მკვეთრი, ბლაგვი ხელსაწყოები არის სითბოს დაგროვებისა და ცვეთის მიზეზი, რამაც ადვილად შეიძლება გამოიწვიოს ხელსაწყოს უკმარისობა.
(5) ტიტანის შენადნობის მაქსიმალურად რბილ მდგომარეობაში დამუშავება, რადგან გამკვრივების შემდეგ მასალის დამუშავება უფრო რთული ხდება, ხოლო თერმული დამუშავება ზრდის მასალის სიმტკიცეს და ზრდის ჩანართის ცვეთას.
(6) გამოიყენეთ ცხვირის დიდი რადიუსი ან ჩამკეტი ჩასაჭრელად და ჩადეთ რაც შეიძლება მეტი საჭრელი კიდე ჭრილში. ეს ამცირებს ჭრის ძალას და სითბოს ყველა წერტილში და ხელს უშლის ადგილობრივ რღვევას. ტიტანის შენადნობების დაფქვისას, ჭრის პარამეტრებს შორის, ჭრის სიჩქარე ყველაზე დიდ გავლენას ახდენს ხელსაწყოს ხანგრძლივობაზე vc, რასაც მოჰყვება რადიალური ჭრის რაოდენობა (ფრეზირების სიღრმე) ae.
გამოქვეყნების დრო: აპრ-06-2022